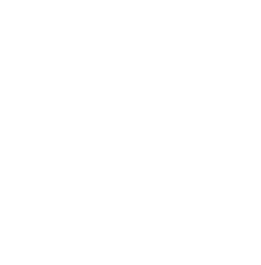
WORKING WITH MATTER
The raw materials used make a difference!
High quality standards and total guarantee are essential components
to obtain artefacts that stand the test of time.
MATERIALS SELECTED
TO GUARANTEE THE HIGHEST QUALITY STANDARDS
Liana Carpenteria specializes in high quality metalwork and artefacts for architecture, museum furniture and civil construction. The use of various materials such as brass, glass powder, metal powder makes the workmanship particularly accurate with unique and superior quality finishes.
Metalworking is an art that has evolved over millennia, skilfully blending craftsmanship and new technologies. Metalworking can take place with the use of different techniques and/or tools, sometimes combined in the process.
Metalworking techniques fall into two types:
- • hot working;
- • cold working.
The terms “hot” and “cold” do not indicate the absolute temperatures of the metals being worked, but simply attribute a value (which is the ratio between the temperature at which the work is being carried out, and the melting temperature of the metal in question) to the state in which that metal is, and in particular its proximity to its melting temperature. If this ratio is less than 0.3, the machining is called ‘cold’, if it is greater than 0.6, it is called ‘hot’; if the ratio has intermediate values, it is called ‘warm’ machining. For example, up to 200 °C steel is cold-worked, while working lead at 25 °C (room temperature) means working it hot.
HOT WORKING
FORGING
Derived from the term forge, a place where the metal piece is heated. It consists of red-hot metal to make it easily deformable. The piece is then beaten with a mallet to obtain the desired shape. This is a very old technique. Today, die forging (stamping) is preferred, whereby the red-hot metal bar is placed on a die and a second die, known as a countermould, is lowered onto it in order to clamp the shape between the two, exerting strong pressure. After forging, the piece is cut into its final shape (blanking) and burrs are removed and corners are smoothed by hand filing (finishing). Hammers and tongs are very strong forged objects that are used as tools.
MOULDING
Casting is used to produce objects that have a very complex shape. Usually, metals with medium or low melting temperatures are melted. The molten metal is thrown into the mould (casting) and waits for it to become solid again through cooling. The mould is opened and the part is finished by removing sprues, burrs and chamfering corners. Cast articles include taps, handles, coffee pots, manhole covers, street lamps.
PRINTING
Then there is moulding, which is done by blowing air with a bellows into a chimney then placing the piece of metal until it turns bright red finally taking a sledgehammer and giving it the desired shape.
COLD PROCESSING
This is only carried out on steel and aluminium sheets. Sheets can be bent or machined to obtain hollow pieces.
BENDING
The deep-drawing operation allows a flat sheet to be transformed into a concave shape, maintaining the average thickness almost unchanged. It is the operation that most stresses the sheet metal during deformation and for this reason requires quality sheet metal. Objects obtained by deep drawing are e.g. saucepans, lids, exteriors of household appliances, car body parts.
IRON
Iron is by far the most widely used metal and alone accounts for 95% of the world’s metal production. It is extracted from ores: pure iron is not found in nature (native). To extract iron from its ores, within which it is found in an oxidized state, it is necessary to remove impurities by chemical reduction of the ore. Industrially, iron is mainly extracted from hematite (Fe2O3) and magnetite (Fe3O4) by reduction with carbon in a reduction furnace at temperatures of around 2000 °C
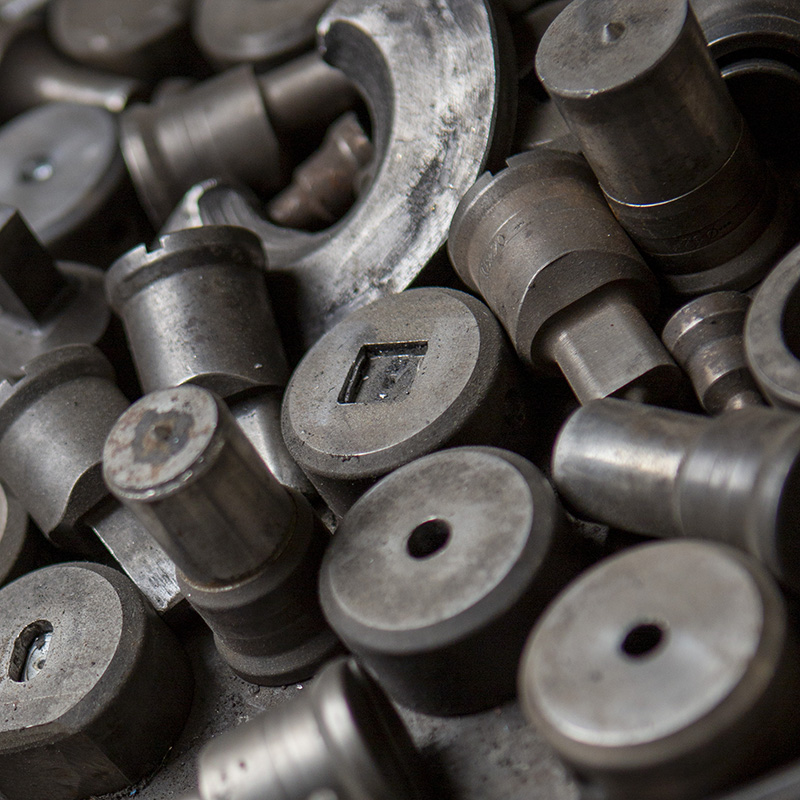
STEEL
It is an alloy of iron and carbon that, thanks to its hard and resistant characteristics, can be used for practically any project. It was first obtained in 1740 by B. Huntsman in Sheffield by melting cemented iron in a crucible and his process was strictly kept secret for many years. Steel interprets the most up-to-date synthesis of engineering and architecture by realizing constructions that translate into profitable investments over time. The variability of construction solutions is significantly increased by the ease with which steel can be combined with other materials. Galvanized, painted, self-patinating and stainless, steel retains its characteristics over time. Many types of steel surfaces do not require any protective treatment.
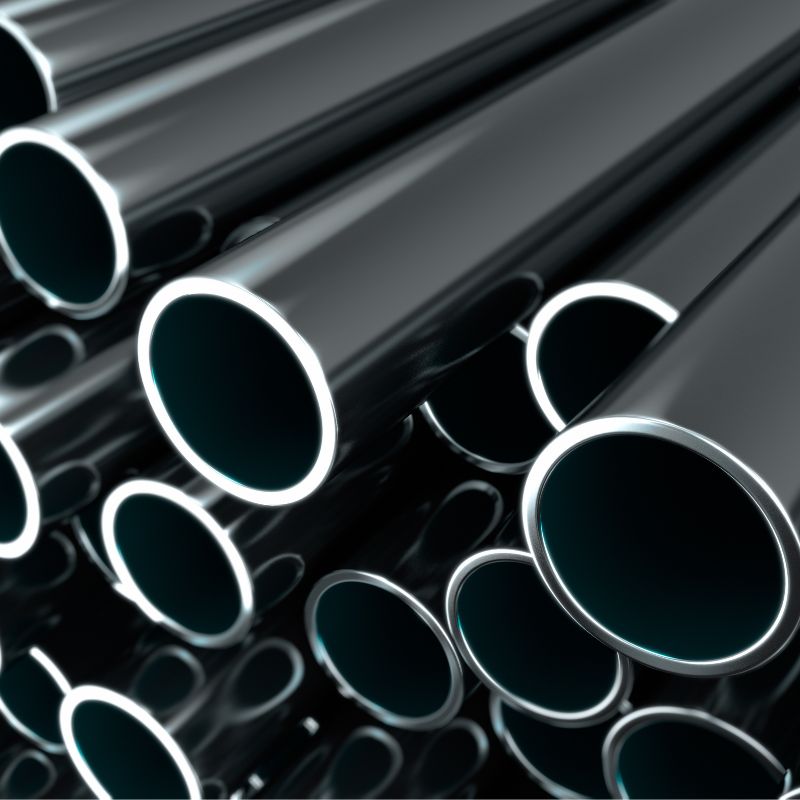
THE BRASS
Brass is an alloy of copper (Cu) and zinc (Zn) with varying percentages of zinc depending on usage requirements for excellent workability. It is a very attractive material due to its good mechanical properties, its resistance to corrosion, its easy workability, etc. The use of the highest quality alloys and materials therefore ensures maximum resistance and safety in the finishing of our products, which are characterised by impeccable workmanship and a handcrafted finish. Decorations and original workmanship are also realised with the use of different materials such as wood, glass and many others.
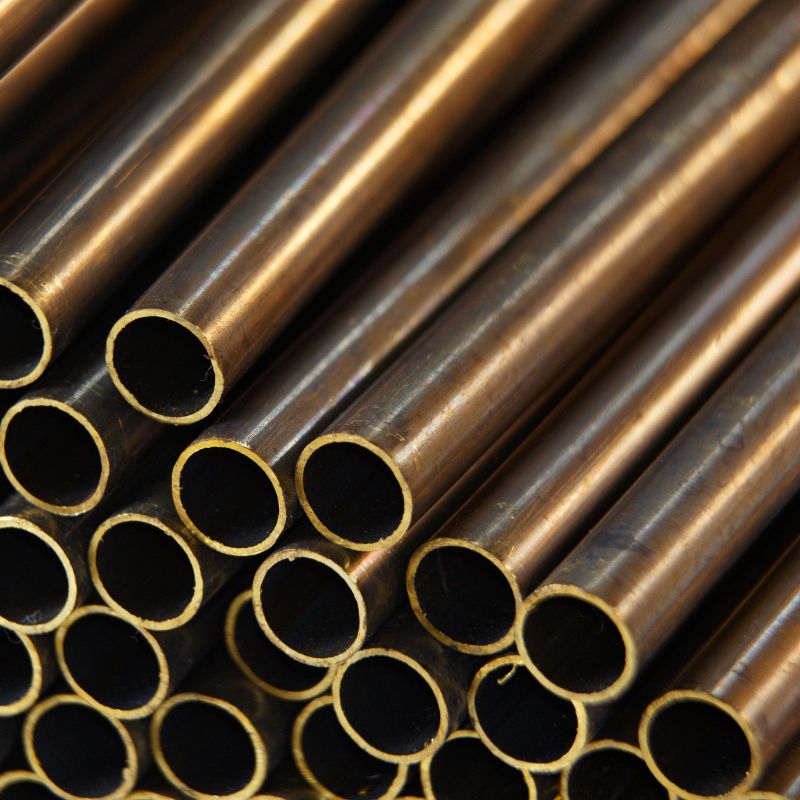
ALUMINIUM
Aluminium is the ideal building material because it is functional, durable and aesthetically appealing. In construction, aluminium products are used for façade cladding and roofing. Choosing aluminium certainly comes from the functionality and efficiency of this material. It should not be forgotten that aluminium is highly valued by architects and planners! It has minimal weight and makes the substructure lightweight and allows building elements to be prefabricated easily.
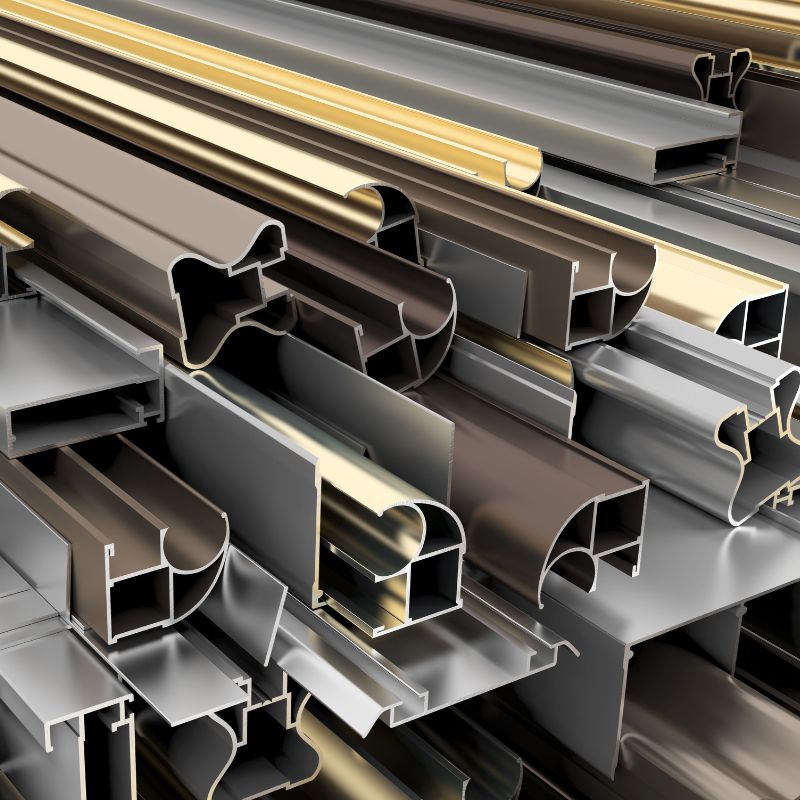